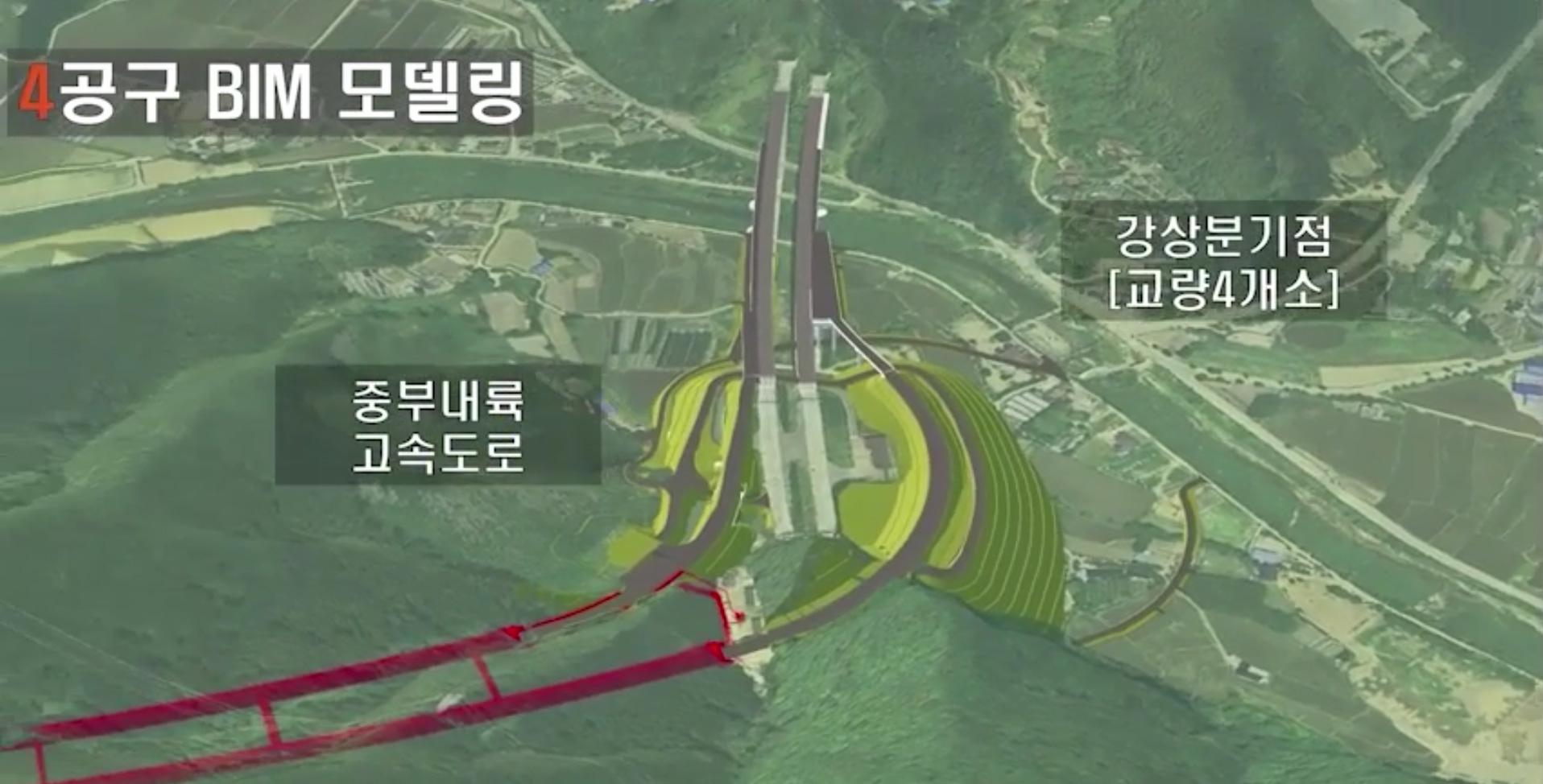
Behind story
The first on-site deployment of Project Works, a BIM 4D/5D platform, was expected to be a tool that could revolutionize the site's schedule and cost management. In particular, the prospect was that construction time could be shortened and cost management could be performed more systematically. However, the early stage of the platform's introduction required some time in the adaptation process, such as optimizing the platform for the site and providing training to operations personnel. In addition, each operations team had a learning period before they became familiar with the new system, but through this series of processes, they began to become increasingly familiar with the system.
BIM's process simulation capabilities were the most significant changes in the field, providing visual visibility into the start and completion of each process, making schedule and cost management easier.
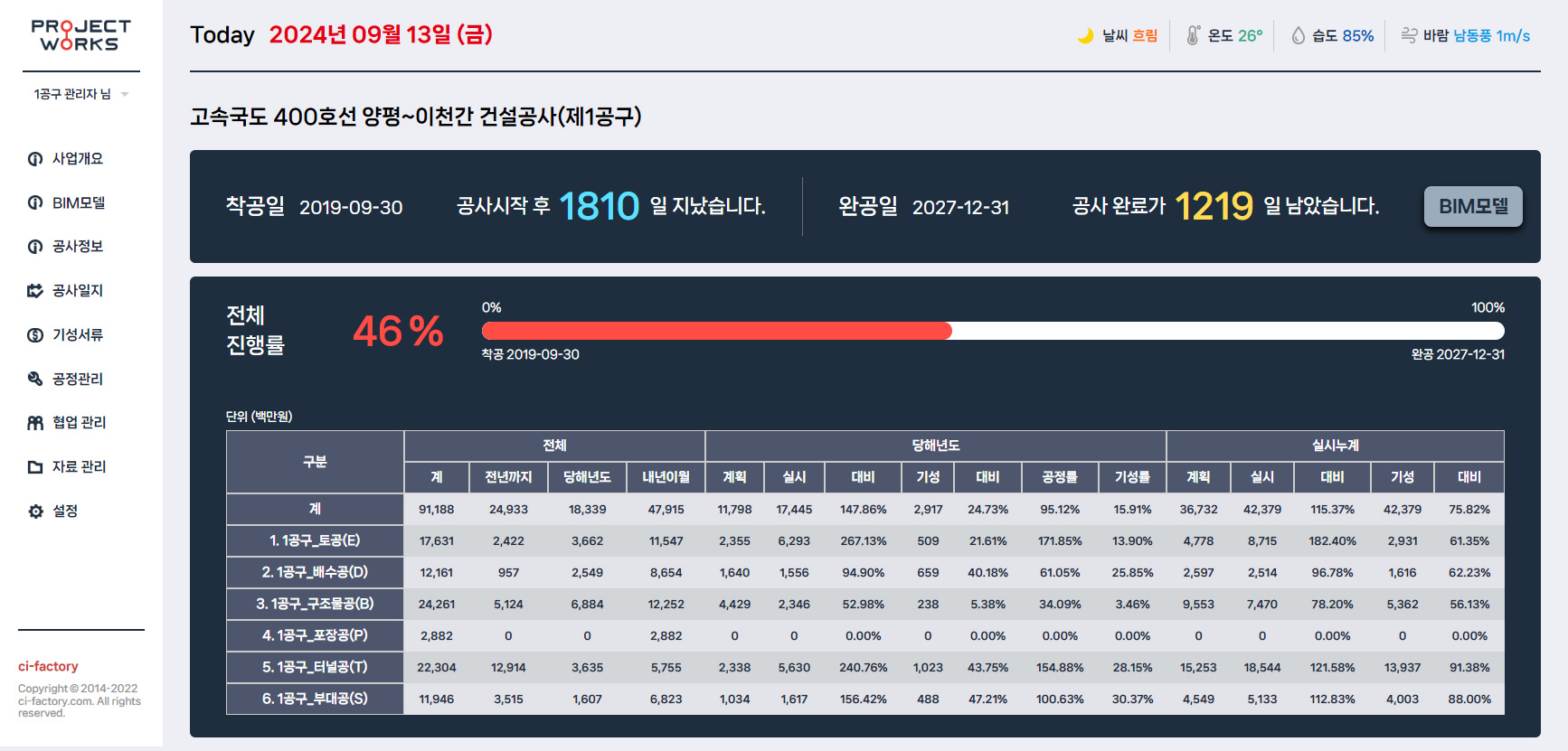
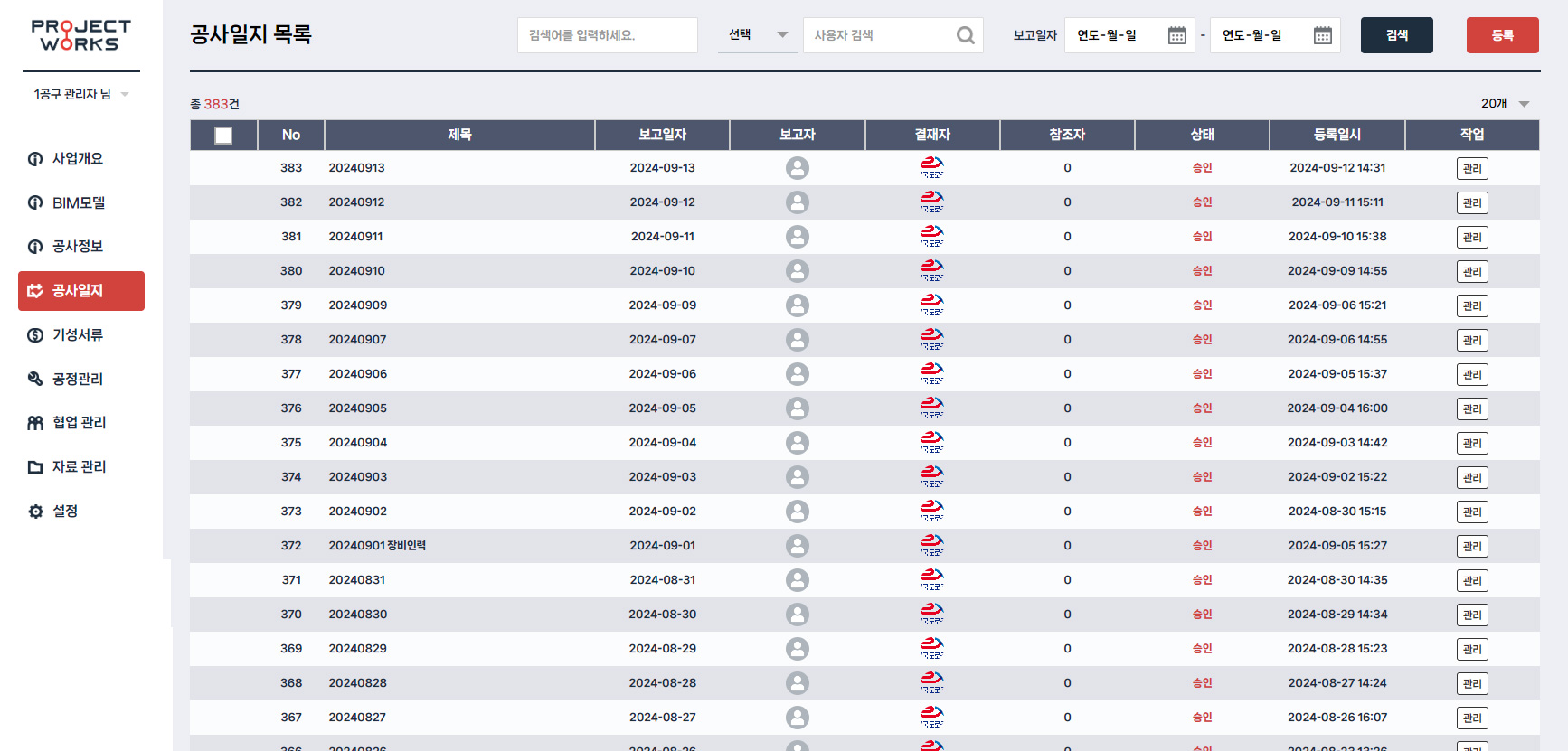
In particular, we were able to predict delays or risks in construction schedules in advance, which allowed us to come up with solutions before problems occurred. We were able to collaborate smoothly between teams and accurately understand the workflow based on the visual data, and manage the budget efficiently. By being able to calculate the expected cost increase in the event of a design change in advance, we were able to help prevent budget overruns and increase cost efficiency for each step by checking and modifying cost items such as material costs and labor costs in real time.
At first, the process of collecting such data on site and immediately reflecting it on the platform was a bit cumbersome, but over time, it got used to it and proceeded more quickly. In addition, communication improved because we could provide reliable data when negotiating budgets with clients.
Project Works was more than just visualizing data, it acted as a tool to strengthen collaboration between field and office teams. Because all stakeholders were able to see processes and costs in real time on the same platform, decision-making speed was accelerated and communication was facilitated. In particular, by providing visualized process planning to field workers, they were able to clearly understand work objectives and timing, which increased work efficiency.
Finding Difficulties and Improvements
When the platform was first introduced, more complex features than expected required time for users to get used to it. In particular, system setup and data input felt complicated at first. However, after a few weeks of use, these difficulties gradually diminished as they got used to the platform. In addition, I realized that if field data was not reflected on the platform in real time, the effect could be reduced. To solve this problem, we needed to improve the data synchronization process between the field and the office.
Development plan
In order to quickly adapt users to unfamiliar platform use, we will strengthen initial training, develop additional offline training and online manuals, and improve the user interface to enable rapid on-site introduction of Project Works. And for smooth reflection of field data, the development team is directly listening to the voices of the field and receiving feedback from each team to derive processing process and UI/UX development plan and is working on improving it, and we are about to launch Project Works 1.8ver.
Conclusion
After applying Project Works to the site for the first time, both schedule and cost management and inter-team communication have improved. There were some difficulties in the initial introduction process, but overall, it helped greatly to increase the success rate and efficiency of the project. In the future, we will continue to develop Project Works into a more stable and user-friendly platform by applying Project Works to more diverse construction projects.